Offset Printing
Offset printing is a common printing technique in which the inked image is transferred (or "offset") from a plate to a rubber blanket and then to the printing surface. When used in combination with the lithographic process, which is based on the repulsion of oil and water, the offset technique employs a flat (planographic) image carrier. Ink rollers transfer ink to the image areas of the image carrier, while a water roller applies a water-based film to the non-image areas.
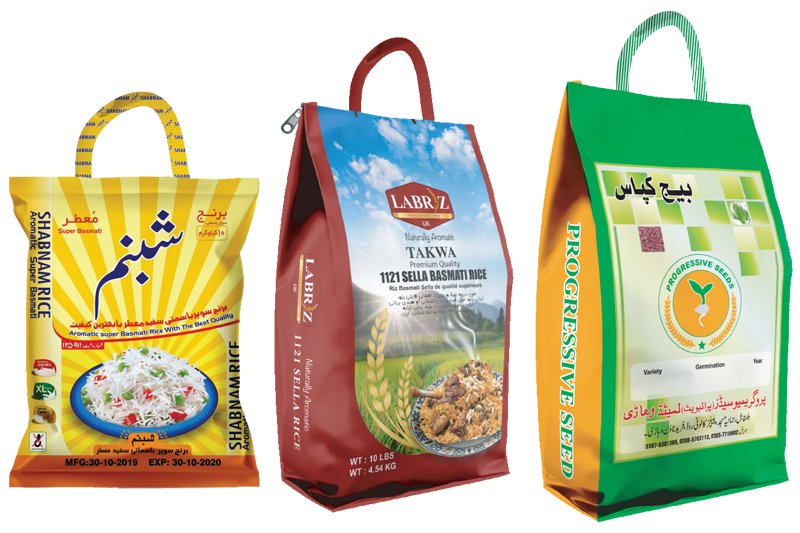
One of the important functions in the printing process is prepress production. This stage makes sure that all files are correctly processed in preparation for printing. This includes converting to the proper CMYK color model, finalizing the files, and creating plates for each color of the job to be run on the press.[8] Offset lithography is one of the most common ways of creating printed materials. A few of its common applications include: newspapers, magazines, brochures, stationery, and books. Compared to other printing methods, offset printing is best suited for economically producing large volumes of high quality prints in a manner that requires little maintenance.[9] Many modern offset presses use computer-to-plate systems as opposed to the older computer-to-film work flows, which further increases their quality. There are two types of offset printing: wet offset and waterless offset. Wet offset lithography uses a mix of wetting fluids (dampening solutions) to manage ink adhesion and to protect non-image areas. Waterless offset lithography employs a different method where a plate's non-image areas are protected via a layer of ink-repellent silicon. Waterless offset lithography is relatively new.[according to whom?] Advantages of offset printing compared to other printing methods include: consistent high image quality. Offset printing produces sharp and clean images and type more easily than, for example, letterpress printing; this is because the rubber blanket conforms to the texture of the printing surface; quick and easy production of printing plates; longer printing plate life than on direct litho presses because there is no direct contact between the plate and the printing surface. Properly developed plates used with optimized inks and fountain solution may achieve run lengths of more than a million impressions; cost. Offset printing is the cheapest method for producing high quality prints in commercial printing quantities; ability to adjust the amount of ink on the fountain roller with screw keys. Most commonly, a metal blade controls the amount of ink transferred from the ink duct to the fountain roller. By adjusting the screws, the operator alters the gap between the blade and the fountain roller, increasing or decreasing the amount of ink applied to the roller in certain areas. This consequently modifies the density of the color in the respective area of the image. On older machines one adjusts the screws manually, but on modern machines the screw keys are operated electronically by the printer controlling the machine, enabling a much more precise result.[10] Disadvantages of offset printing compared to other printing methods include: slightly inferior image quality compared to rotogravure or photogravure printing; propensity for anodized aluminum printing plates to become sensitive (due to chemical oxidation) and print in non-image–background areas when developed plates are not cared for properly; time and cost associated with producing plates and printing press setup. As a result, very small quantity printing jobs may now use digital offset machines. Every printing technology has its own identifying marks, and offset printing is no exception. In text reproduction, the type edges are sharp and have clear outlines. The paper surrounding the ink dots is usually unprinted. The halftone dots can be hexagonal though there are different screening methods.
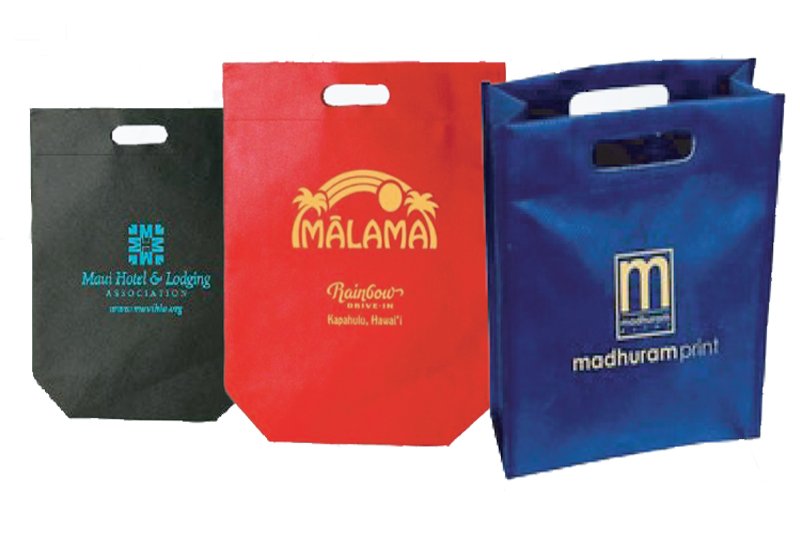